HPMSM Processing 101
Process Routes for High Purity Manganese Production
Most of the world’s commercial production of high purity manganese is based in China and this summary contains information from operating Chinese production plants. High purity manganese production is based on a process hierarchy that is followed by all producers including those in the west.
- Ore is leached, and impurities are removed to produce a purified manganese sulfate solution using a process like that shown in Figure 1.
- Purified manganese sulfate solution serves as the electrolyte to produce standard-grade electrolytic manganese (EMM) or electrochemical manganese dioxide (EMD). It is also the starting solution for crystallizing regular-grade manganese mono-sulfate (MSM) as shown in Figure 2. EMD and CMD are components in non-rechargeable alkaline batteries. Manganese sulfate monohydrate (MSM) is used as a fertilizer supplement and in other miscellaneous applications. EMM is used for alloying
- Higher purity products, HPEMM and HPMSM, are produced by employing extra refining steps to lower the critical impurities that affect Li ion battery performance. Figure 2 shows the three process routes, 1, 2, and 3 and each is summarized in the description below.
The first high purity method is based on upgrading electrolytic manganese metal (EMM). About 1.7 million tons annually of EMM is currently being produced globally mainly for use as an alloying additive in the stainless steel and aluminum industry. High purity electrolytic manganese (HPEMM) is made in smaller quantities by further purifying some of the EMM electrolyte to lower the levels of the so-called alkali metals Ca, Mg, Na, and K which, as a group, are harmful to battery performance. HPEMM is then dissolved in sulfuric acid and crystallized as HPMSM. Additional refining takes place in the crystallization step.
In the second high purity route, electrolytic manganese dioxide (EMD) is the primary product, which is sold for use in non-rechargeable, Duracell-type alkaline batteries. HPMSM is known to be being produced by at least one Chinese company that diverts a fraction of the EMD ore for separate treatment before crystallizing the HPMSM product.
In a third method, regular grade manganese sulfate monohydrate crystals (MSM) are produced in global quantities of about 400,000 tons annually primarily for fertilizer applications. A minority of this output is being refined to a high purity version (HPMSM) by re-dissolving the crystals and lowering the impurity content in the concentrated manganese sulfate solution before re-crystallizing the high purity product.
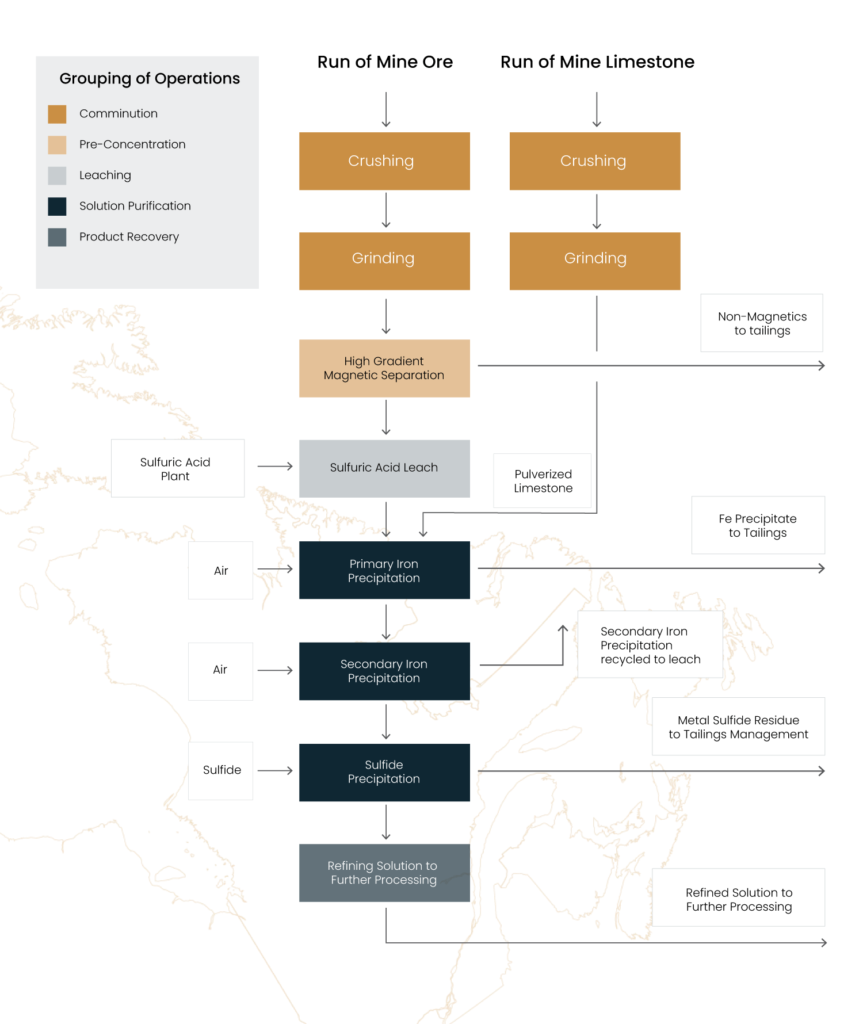
Figure 1. Production of Purified Manganese Solution from ore
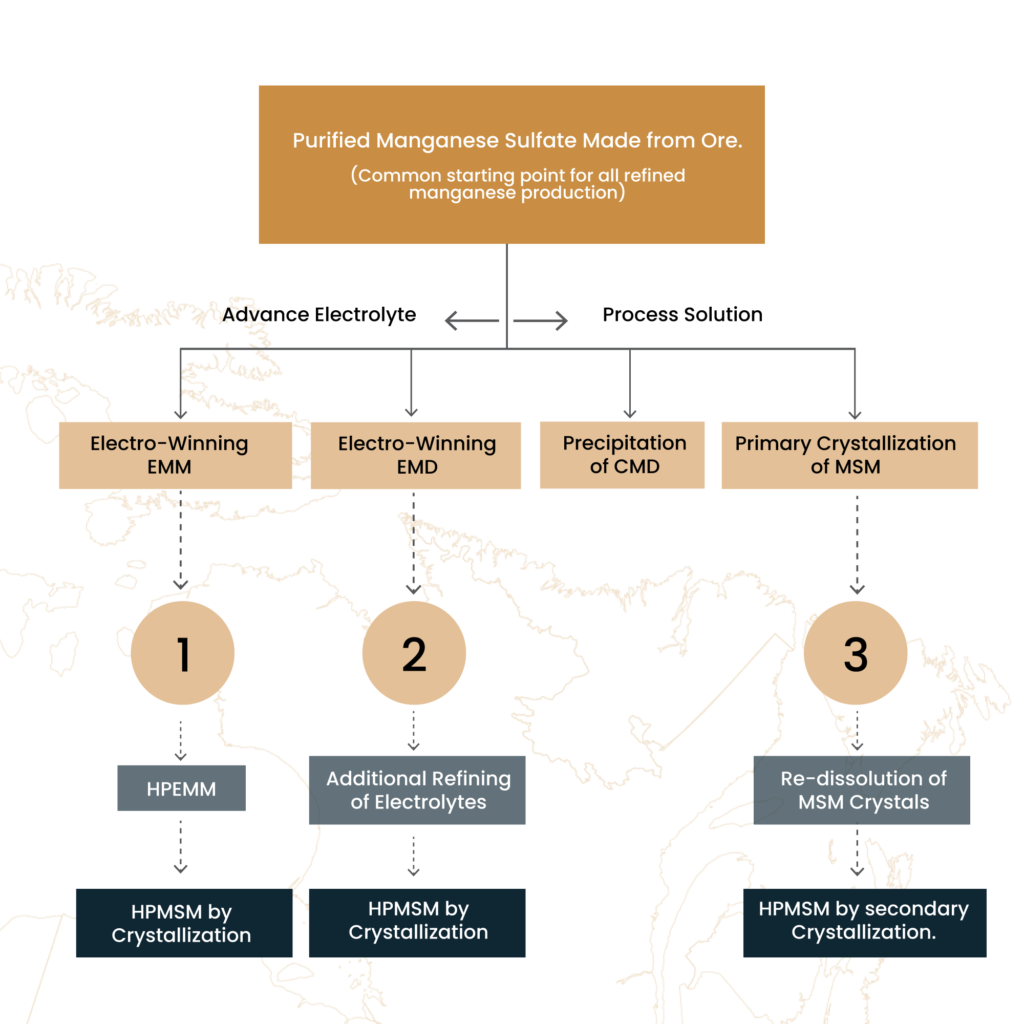
Figure 2. Production routes for refined manganese products.
It should be noted that the production of battery electrodes using sulfate-based metal solutions is undergoing scrutiny because the sulfate component is ultimately discharged as waste after the battery metal is precipitated. The use of metal chlorides is being studied as a potential replacement for sulfates because the (hydrochloric) acid can be recycled. Although this concept is only at the R&D stage, it would be a consideration favouring HPEMM production to prepare either high purity sulfates or chlorides.
China has relatively poor-quality domestic deposits of manganese, typically having grades below 30 percent manganese grade (pyrolusite) with elevated levels of impurities. Most Chinese ferro-manganese, ferro-silicon and refined manganese products are made from imported pyrolusite ore. The main suppliers are Australia, South Africa, and Gabon. Pyrolusite contains manganese in oxidized form and ore grades of at least 35 percent manganese are needed to justify ocean shipping and additional inland transportation cost, as most of the processing takes place in the Northwest of China.
To make oxidized manganese ore soluble in acid it must be dried and pre-treated by reduction, often referred to as calcining. Calcined ore is dissolved in sulfuric acid as the first step in refining the manganese to a value-added product. Chinese manufacturers follow the flow sheet shown in Figure 1 with reduced pyrolusite ore as feed stock.
The three methods described produce HPMSM containing 32 per cent manganese, which is the working standard for HPMSM. The crystallization process is fuel-intensive because large quantities of water must be evaporated and the preparation of concentrated manganese solutions to feed the crystallization step is a key consideration in the process design. The use of HPEMM as the starting material yields pure, concentrated manganese sulfate solutions with the lowest energy consumption per ton of Mn in HPMSM. On the other hand, EMM/HPEMM production consumes large amounts of electric power, and the choice of process route may be influenced by the local, long-term supply cost for these two items.
Low-Carbon Production of Refined Manganese
It is apparent from the foregoing discussion that much of the carbon can be eliminated from the refined manganese production by processing un-oxidized manganese ores such as carbonate which dissolve directly in sulfuric acid without the need for reduction.
The manganese carbonate mineral, known as Rhodochrosite (manganese carbonate) ore is ideal to produce refined manganese by low carbon methods. However, in some deposits rhodochrosite ore is mixed with pockets of manganese dioxide which complicate subsequent purification. Plymouth ore is made up of a uniform 90 per cent manganese carbonate.
The presence of iron in manganese carbonate ore makes it amenable to high intensity magnetic separation. This cost-effective physical method lowers the quantity of iron to be precipitated later in the solution purification process. An added benefit is that some of the alkali compounds present in the ore are also removed with the iron and this reduces the consumption of acid during dissolution. Acid consumption is a major cost factor in refined manganese production and is discussed later.
The Purification Process
The process diagram in Figure 1 shows a generic flow sheet with the conventional steps needed to produce a manganese sulfate solution suitable for final refining. Almost all refined manganese processing, including reduced pyrolusite ore in China, follows this route. Competitive advantages for the Plymouth ore in this flowsheet are pointed out in the description of the process operations below.
Mined manganese ore is subjected first to the relatively low-cost operations of crushing and grinding and, in the case of Plymouth ore, magnetic separation. This yields a pre-treated ore ready for the downstream process steps.
Acid Leaching
Sulfuric acid dissolves manganese carbonate ore readily whereas (reduced) pyrolusite requires a two-stage leaching procedure to achieve high extractions from the ore. Iron and
other constituents co-dissolve with the manganese values and these have an influence on processing costs. Sulfuric acid consumption is increased by iron dissolution and by the solubilizing of worthless alkali compounds such as aluminum and magnesium present in the ore. The dissolution of metals other than manganese represents unwanted acid consumption and the total acid consumed is usually multiples of that required for manganese alone. Acid is therefore an important cost item in refined manganese production. This has become even more of an issue in the past year as acid prices have increased sharply due to the rising price of sulfur used for acid production. Sulfur prices are expected to remain high because it is also used to produce acid for the dissolution of nickel from laterite ores. This is an expanding market driven by projections of EV demand and sulfur prices can be expected to remain at elevated levels for the foreseeable future.
Some mitigation of the acid expense is possible by substituting pyrite (FeS2) for sulfur in sulfuric acid production. A similar benefit is possible if the manganese purification process can be sited close to an existing acid production facility since this will eliminate the capital cost of an acid plant.
Treated leach slurry is filtered to separate the barren leach residue from the manganese process solution. The residue is washed thoroughly and becomes the part of the tailing. The manganese solution goes forward for the removal of contaminants.
Iron Removal
Iron is a common constituent of all manganese ores, and it is removed by precipitation from the manganese solution produced in the leaching stage. To be precipitated iron must first be converted to its oxidized (ferric) form and an oxidant is needed. In most plants the oxidant is air (oxygen) which is fed to the reactor. However, iron removal by air/oxygen is slow and requires two stages and five hours or more for completion. Thus, there is an indirect penalty in the higher capital cost for the construction of larger precipitation vessels to allow for extended residence times. Alternative methods that remove iron more efficiently allow a more compact precipitation system and hence a saving on capital cost.
Manganese dioxide can be used to oxidize iron and has the benefit of adding manganese values to the solution as iron is removed. If it can be procured at a reasonable price and does not introduce additional impurities, manganese dioxide may be a useful reagent for iron removal.
Currently investigating our own iron removal method, which can eliminate iron in about one quarter of the time required by the air/oxygen method. High grade magnetic separation (HGMS) equipment and method have been shown to produce satisfactory upgrading of the ground ore to a concentrate with ~15.6 percent average grade of manganese at almost 99 percent manganese recovery. Of equal importance to the process economics is the rejection of part of the worthless acid-consuming minerals by the system. To date most leach tests have been run on composite ore samples. Leaching manganese concentrate, rather than ore, decreases acid usage since magnetic separation rejects some of the acid-consuming minerals.
A further competitive advantage is the fact that about two-thirds of the iron in the Plymouth deposit is present as haematite (Fe2O3). Haematite iron is already in the ferric state and does not need oxidation. The remarkably constant 1:1 relationship in duplicate samples taken from drill cores for both iron and manganese in the Plymouth deposit is shown in Figures 3 and 4. This demonstrates the uniformity of the ore body over a range of manganese grades and indicates substantial homogeneity exists within the core samples and the deposit.
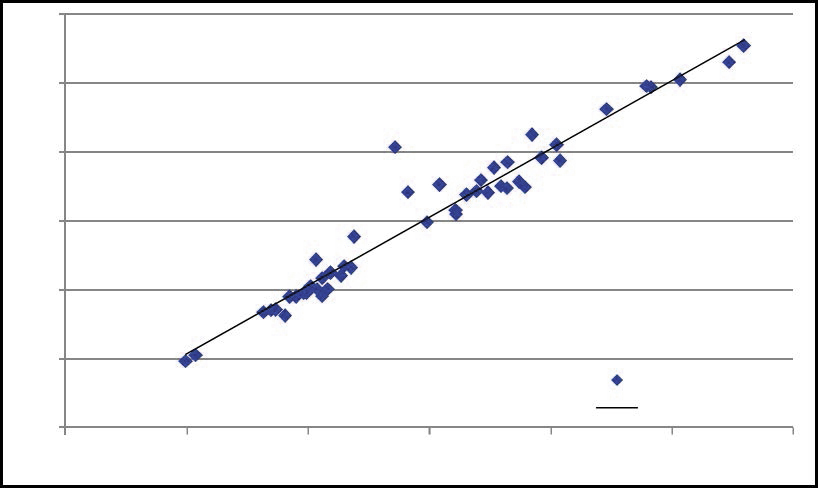
Figure 3: Fe2O3 content in 47 Plymouth core samples.
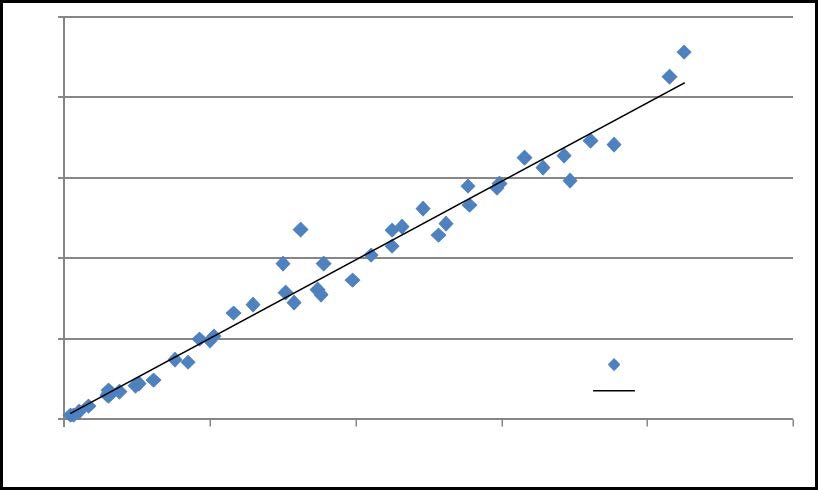
Figure 4: MnO content in 47 Plymouth core samples.
Heavy Metal Removal
Iron–free manganese solution still contains the group of contaminants known as heavy metals. These include copper, zinc, nickel, and cobalt which are present in relatively small quantities and are removed by precipitation as their sulfides. This process must not leave residual impurities in the manganese solution when the heavy metals have been removed. Precipitation agents such as barium sulfide are used because barium forms an insoluble sulfate, and any excess barium is rejected with the heavy metal sulfide precipitate and is not transferred to the manganese solution. After the manganese solution is purified of iron and aluminum, the levels of each of these metals is in the range of 1-10 ppm and they are removed by sulfide precipitation. It is important that the precipitation reagent that does not introduce any ions that may contaminate the manganese solution.
If EMM is to be produced, ammonium sulfide can be used as the precipitant because ammonium sulfate left in the manganese sulfate solution is also present in EMM electrolyte.
In crystallization mode this is not possible and the alternative is to use reagents such as barium sulfide because the reaction product barium sulfate is insoluble and is discarded with the heavy metal precipitate.
After filtration of the heavy metal sulfides, the manganese sulfate solution contains only small quantities of calcium and magnesium as the remaining impurities.
Final Refining
Despite the relatively low levels of calcium and magnesium in the manganese sulfate following heavy metal removal, the elimination of these two impurity elements is challenging if the objective is to proceed to the direct production of MSM without an intermediary EMM stage. In this case, the final step in the production method is subject to several competing technologies currently being investigated by various Western and Chinese companies as the final purification step for producing MSM or its high-purity equivalent.
Proprietary techniques include evaporation of the manganese solution to about 30 percent of its volume with filtration of the precipitated calcium and magnesium. The purified solution is then cooled and crystallized to make the final MSM product. Evaporation is an energy-intensive process.
Calcium and magnesium can be separated from MSM crystals by washing with concentrate sulfuric acid. Six cycles of crystallization and washing are needed to meet the required specification.
The elimination of calcium, magnesium and other impurities is simplified if there is co-production of EMM. Thus, manganese is precipitated in bulk from solution as manganese carbonate, using ammonium carbonate. This leaves most of the unwanted calcium and magnesium in the ammonium sulfate filtrate. This is recycled to an EMM circuit where ammonium sulfate is in the electrolyte and the calcium and magnesium can be removed from the electrolyte bleed stream. Purified manganese carbonate is re-dissolved in acid to form the MSM crystals.
A third method uses ammonium fluoride to precipitate calcium and magnesium fluorides, and this requires an EMM circuit is present. The value of an HPEMM facility in the removal of calcium, magnesium and other impurities from magnesium sulfate is apparent. This advantage, together with acid recovery, explains why electrolytic facilities are frequently used in the co-production of HPMSM.
There are several other methods being evaluated either at the laboratory or pilot stage. Most of the new technical papers on the subject are issued in China.
Operational Costs
Almost all refined manganese is produced by the following sequential process steps (refer to Figure 1)
- Mining of ore
- Crushing and Grinding.
- Pre-treatment of the ore by reduction or magnetic separation.
- Leaching of the treated ore in sulfuric acid
- Iron removal.
- Heavy metal removal.
- Final refining.
The costs associated with these operations vary with the nature of the ore and the location of the processing site. The ore characteristics are largely fixed and the main economic drivers for the purification steps in a low-carbon process are:
- Sulfuric acid.
- Hydro-electric power if EMM production is contemplated.
- Fuel for heating solutions or crystallizing products.
- Transportation and logistics efficiencies if there is off-site processing.
The siting of a production facility at a location offering financial incentives is an additional economic factor to be considered.
Co-production of HPEMM is an important strategic consideration in the preparation of HPMSM. One of the most compelling attributes of EMM production is that it produces sulfuric acid as a by-product. Acidic electrolyte is recycled to the leaching step to pick up manganese from the ore thereby lowering the acid requirement from an acid plant. The quantity of acid recycled from the electrolysis process is only equivalent to the manganese dissolved and make-up acid from an acid plant is still needed to provide the additional acid consumed in co-dissolving iron and the other alkali elements in the ore. Nevertheless, given the importance of minimizing acid consumption at a time of high sulfur prices, the inclusion of an electrolytic manganese circuit offers the triple advantages of reduced acid usage, simplification of the final purification procedure and a marketable product for alloying applications.
As a final point, the production of EMM offers the choice of preparing alternative manganese salts by using different acids for dissolution. The production of sulfate salts for battery use is beginning to be scrutinized for its waste impact. When manganese (or nickel or cobalt) sulfates are used in the manufacture of precursor oxides for battery electrodes, all the sulfate is rejected as waste, either as a solid residue of calcium sulfate or as sodium sulfate liquid effluent. The magnitude of this problem is increasing as Li ion battery production rises. Using chlorides of these metals, acid can be recycled and there is essentially no waste. Chlorides are starting to be investigated as alternative feed materials.